In supply chains with high sanitation requirements, such as food manufacturing and pharmaceuticals, pallets can be a major concern. Although pallets are not primary packaging in these industries—meaning they do not come into direct contact with the products they carry—they can still pose significant contamination risk to the facilities and products for which they’re used. Wood pallets, in particular, have come under intense scrutiny many times over the last decade as the cause of various FDA recalls. As a result, many food and pharmaceutical manufacturers as well as retailers began looking for non-wood pallet materials to avoid the risk of contamination, and the pressure to convert to more hygienic pallets continues to mount. Here, we examine the various types of contamination hygiene-sensitive pallet users must avoid, and compare the level of risk that wood, HDPE plastic, and fiberglass composite pallets pose to users.
Foreign Material Risk from Pallet Debris
In 2019, the U.S. Department of Agriculture’s (USDA) Food Safety and Inspection Service (FSIS) began developing guidelines for meat and poultry industry operators after noting a significant increase in the number of recalls for contamination with foreign materials. The meat and poultry industry is certainly not alone in this challenge, as foreign materials in finished products is one of the top drivers of consumer complaints across all sectors of the food industry.
The risk posed by foreign materials is not limited to inclusion in finished product. Broken pieces of wood or plastic pallets can tear open soft primary packaging such as boxes and bags, as can nails or other fasteners used to manufacture these pallets. Damage to the primary packaging leaves the product inside vulnerable to contamination by any number of substances during distribution, even if the piece of pallet material or fastener does not end up inside the finished product. Spills of damaged product create additional hygiene issues if the product leaks in storage or during transportation. In the case of food products, spills can also provide an attractive food source for pests within the facility or truck. Managing this risk when using wood pallets or older plastic pallets that have become brittle is a significant challenge for food safety and quality assurance professionals across the food sector.
When discussing foreign material risk, wood pallets deservedly receive the majority of scrutiny. But HDPE plastic pallets present a similar risk as they age or are exposed to temperature extremes in the cold chain. The plastic becomes increasingly brittle with use and exposure, and more susceptible to breakage and splintering.
In contrast, fiberglass composite pallets are made from a non-shedding material that does not produce dust or debris, eliminating risk of foreign material from the pallets themselves. Even at the end of the useful life (around 150 uses), fiberglass composites have been shown to maintain structural integrity in independent testing by Virginia Tech1. This composite, called Fiberglass Reinforced Plastic (FRP), is a very common material used to manufacture items that must withstand heavy weight, wide temperature fluctuations and impact without splintering. The material is commonly used in bath tubs and shower stalls, doors, composite decking, swimming pools and hot tubs, boats, snow and water skis, to name a few.
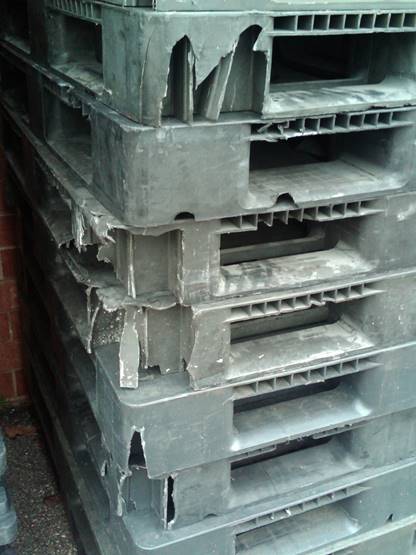
The (Mostly) Unseen Pallet Hygiene Threats: Toxicity, Pathogens and Pests
When discussing pathogens and pests, it should come as no surprise that wood presents the biggest challenge. Its absorbent nature allows wood to become an attractive host for bacteria, mold, and other microorganisms once it absorbs moisture, a common occurrence in food and pharmaceutical supply chains. Not only can visible liquids such as water from melted ice or even liquid products seep into the wood, swings in temperature and humid environments can create invisible condensation within the wood fibers. Also, users attempting to clean visible debris from wood pallets by spraying with water inadvertently create a host environment for invisible pathogens and mold spores.
Toxic liquids from previous users may be absorbed into wood pallets, with future users none the wiser. In many cases, these chemicals such as anti-fungal treatments are intentionally placed on the pallets in order to decontaminate them or prevent contamination. Wood pallets are both hard to clean and simple to accidentally contaminate, which is why many users seek pallets made from alternative materials, such as plastic or fiberglass composite. Both HDPE plastic pallets and fiberglass composite pallets are made from non-porous materials, which is a huge advantage over wood pallets from a hygiene perspective. However, although plastic pallets do not absorb moisture or chemicals, they cannot match the fiberglass composite pallet’s inherent antimicrobial properties.
The RM2 BLOCKPal is fully encased in a polyurethane composite which is impervious to bacterial contamination and meets the ASTM G21 anti-fungal standard and are ISPM-15 exempt. Further, many plastic pallets must be treated with carcinogenic fire-retardant chemicals in order to meet the FM 4996 fire safety standard, whereas fiberglass composite pallets are naturally fire retardant and require no additional carcinogens or neurotoxins to meet the FM 4996 standard. In fact, even though pallets are not required to meet the standards of food contact packaging, RM2’s fiberglass composite pallets are certified by the NSF to meet the standards for FDA GRAS and EU Food Contact materials.
Taking Action: Pallet Cleaning and Sanitation
With all the hygiene risks outlined above, it’s no wonder many pallet users want to clean their pallets before use. Unfortunately, in the case of wooden pallets, washing can remove visible debris but increase likelihood of other contamination. In addition to adding moisture, high pressure sprayers can compromise the integrity of the wood surface, making it even more susceptible to pathogens, pests, and mold. The use of sanitizing chemicals can present the same issues, as well as contaminate the wood with unsafe chemicals for future users.
Both fiberglass composite pallets and plastic pallets can be sprayed down with water or sanitizing chemicals to remove debris and eliminate surface pathogens, using an appropriate cleaning agent. However, users who choose to sanitize pallets themselves bear the risk if pallets are not cleaned properly. Unfortunately, plastic pallet poolers typically do not offer sanitization services, and thus users are forced to try to clean to strict standards themselves.
Fortunately, RM2 offers pallet cleaning services for hygiene-sensitive users. The company operates three strategically located pallet cleaning facilities in the United States, each with the capacity to wash over one million RM2 pallets each year. The pallets are washed in standardized machines in an automated two-step process that ensures consistent cleaning and drying of the pallets, including 140° F water with high-pressure jets located at the top, middle, and bottom of each pallet, using environmentally-friendly, non-toxic Simple Green detergent. The pallets are rinsed in clean water using additional high-pressure jets to remove any detergent residue, then dried with mechanical blowers prior to exiting the machine. After the wash process is complete, pallets are swabbed to confirm acceptable ATP readings.